I built this for my daughter to ride around the backyard. Its about 1:9 scale with the tracks 6.25″ apart. It uses a 700w 900kv motor direct driving one of the wheels. The track is made of .5″ square steel tubing with a .0625 wall thickness and the ties are 1×2 wood. It can tow at least 175lbs.
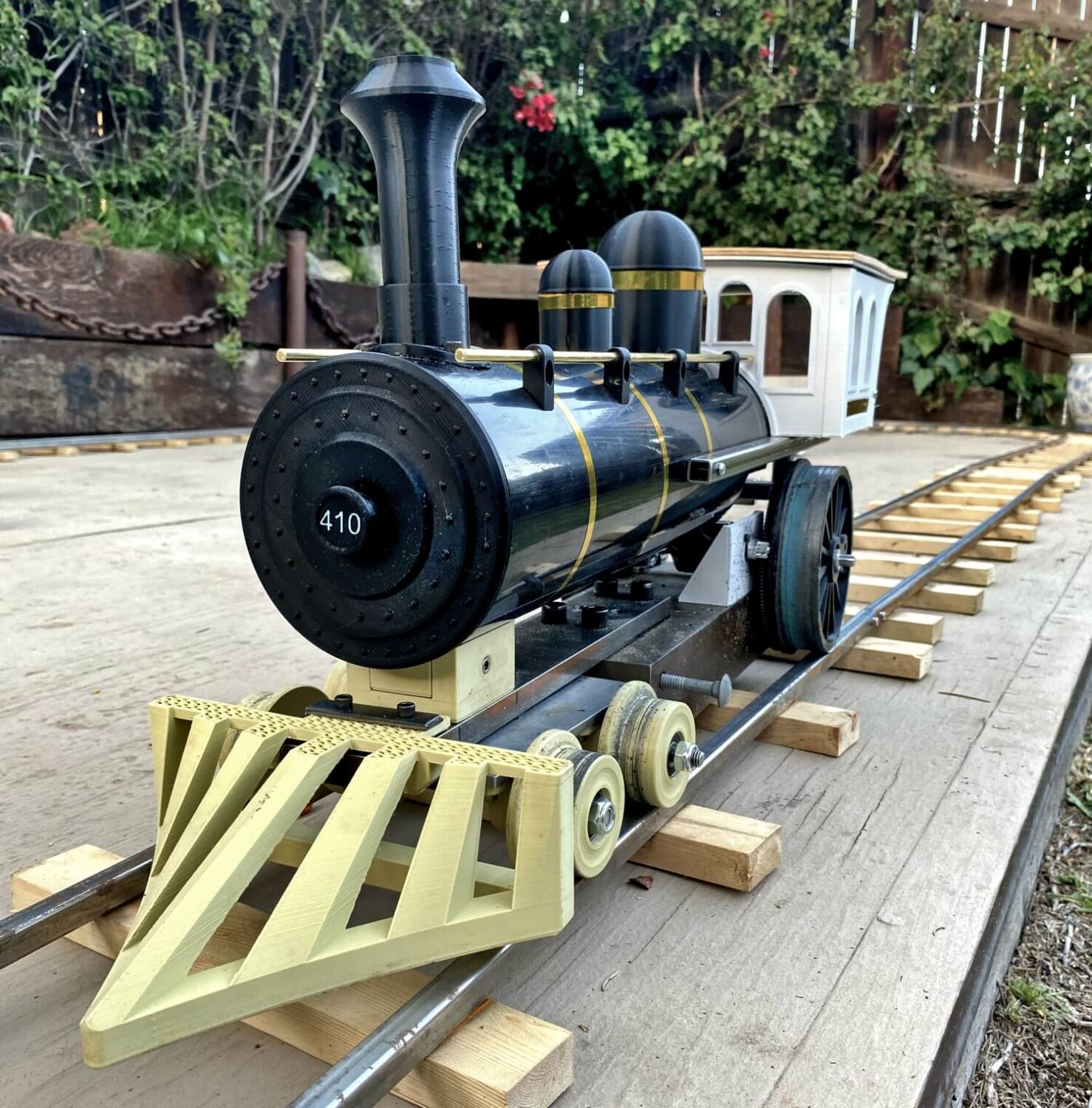
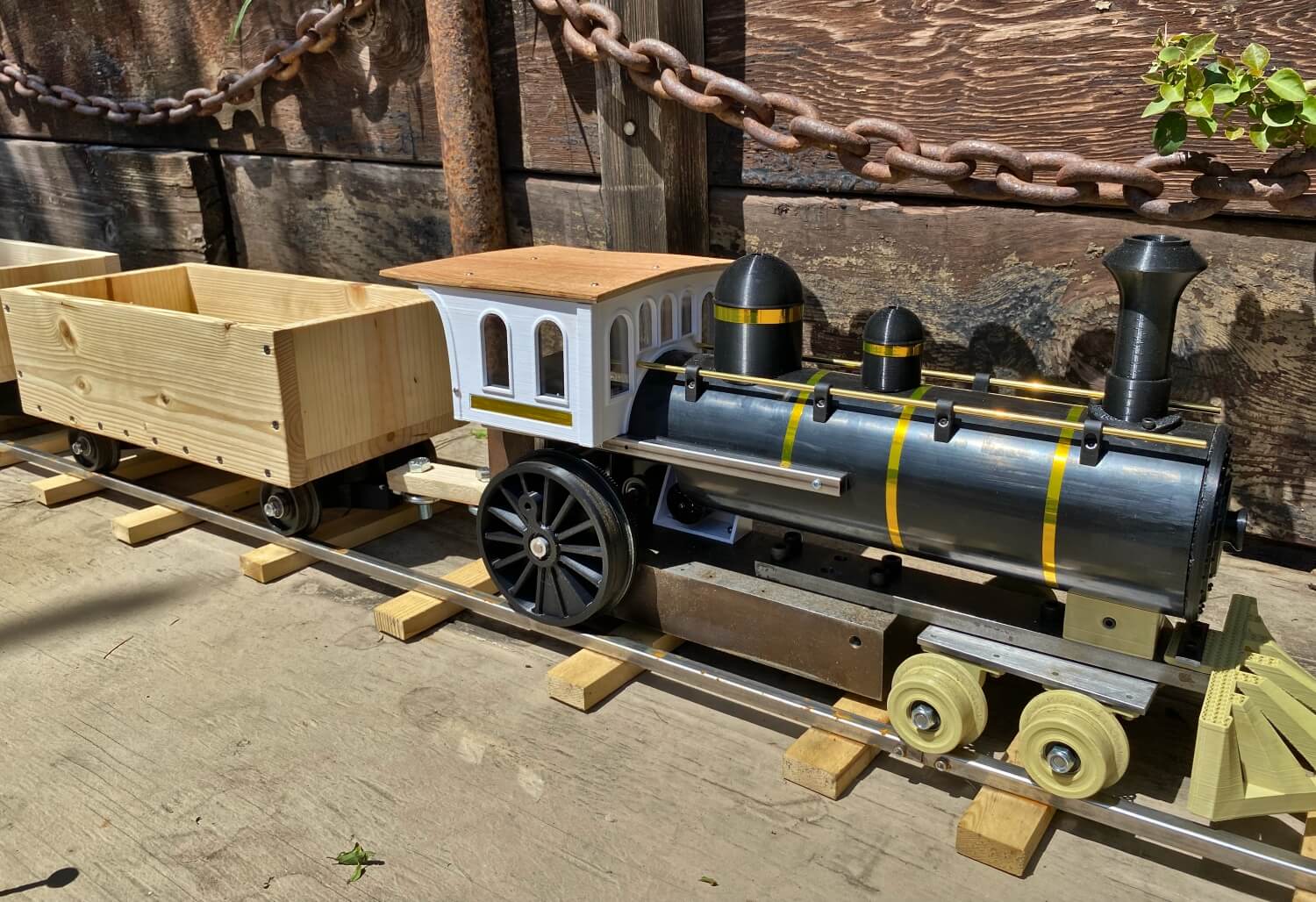
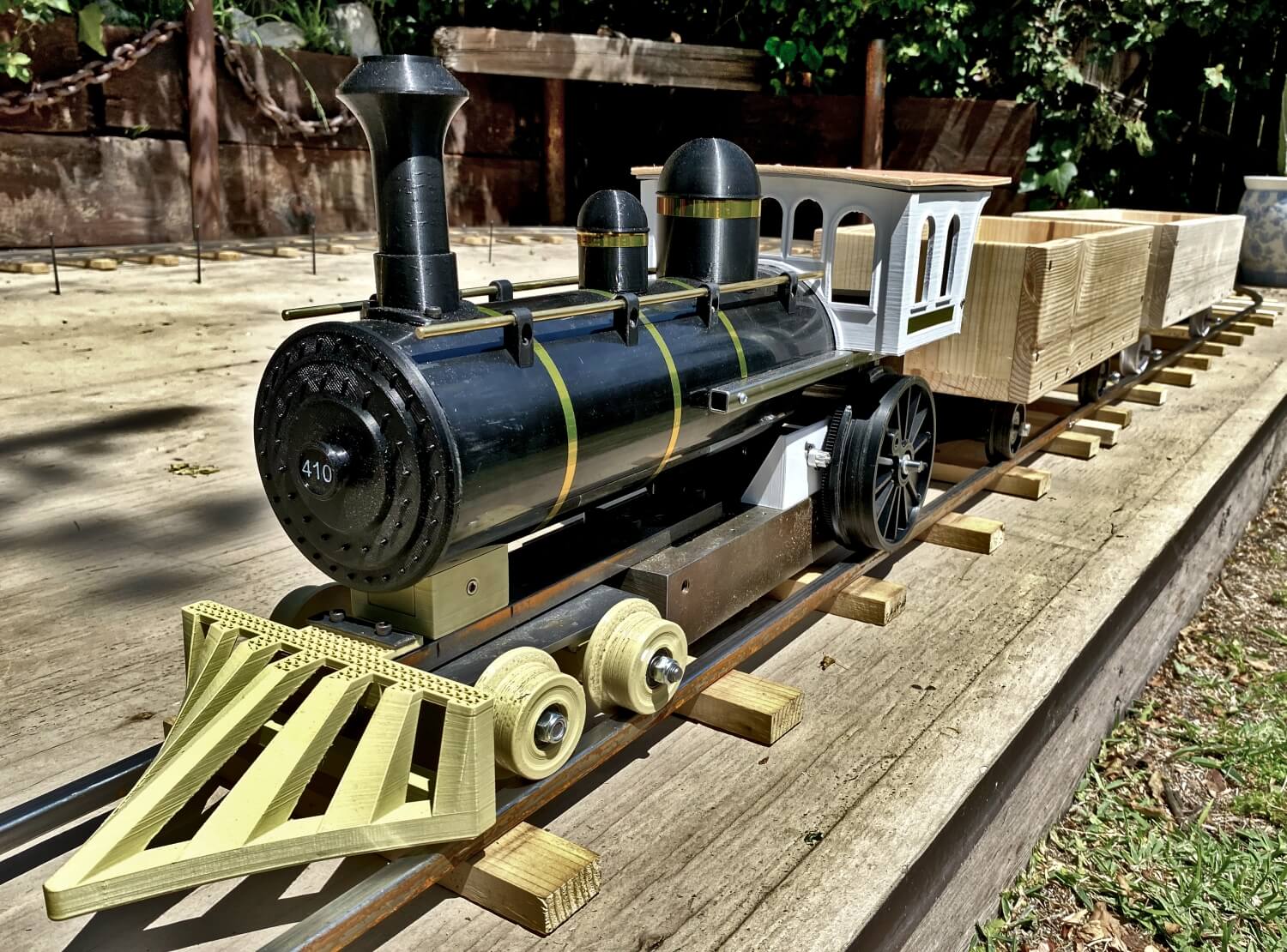
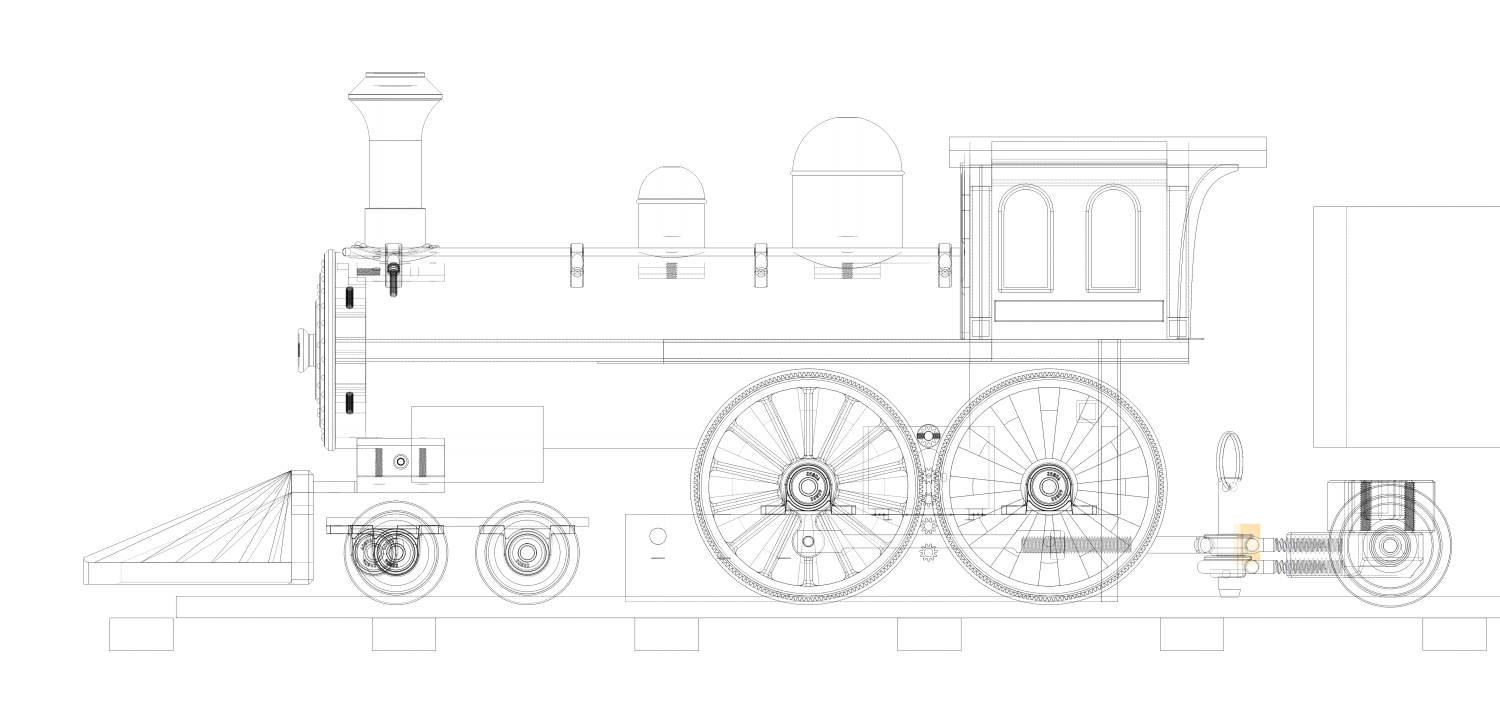
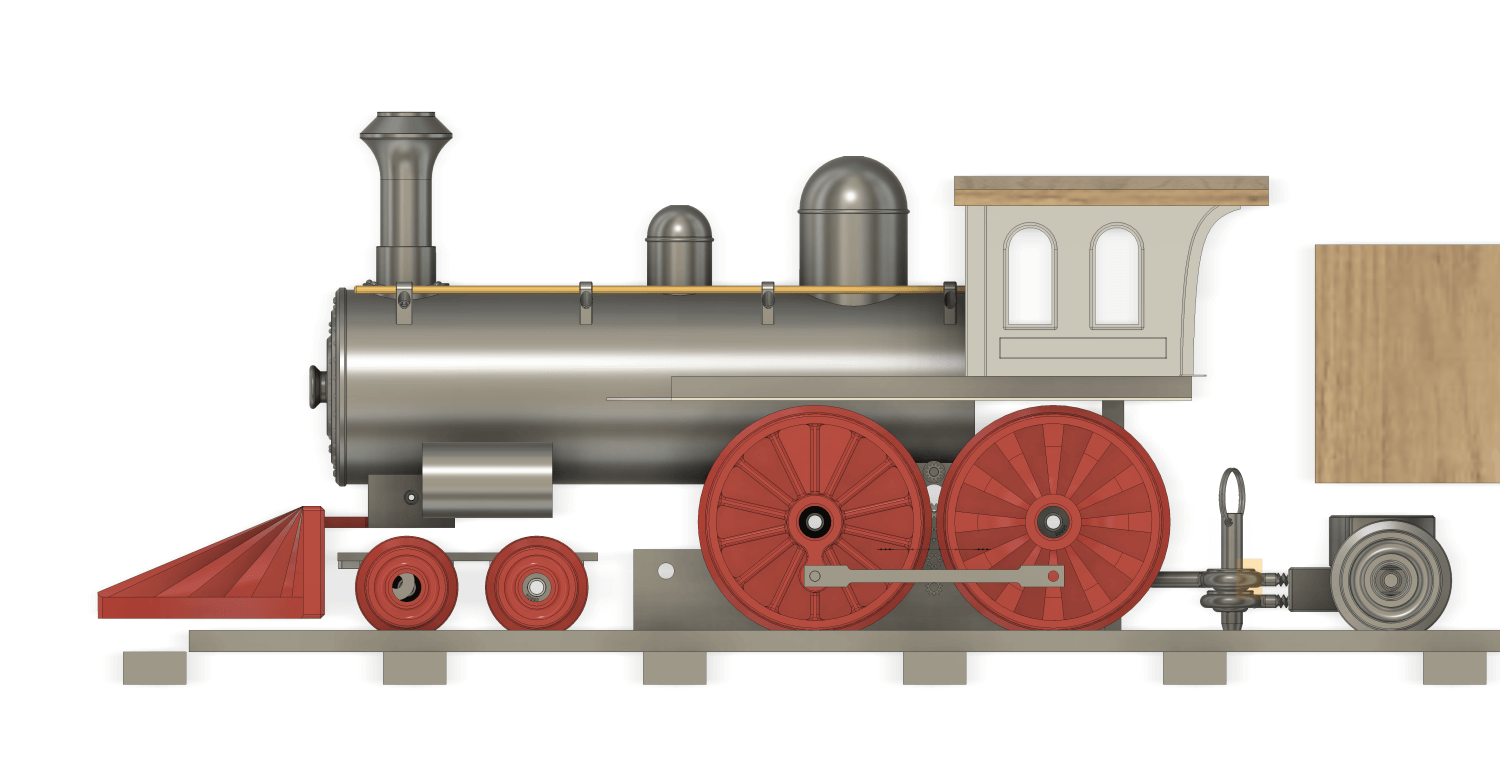
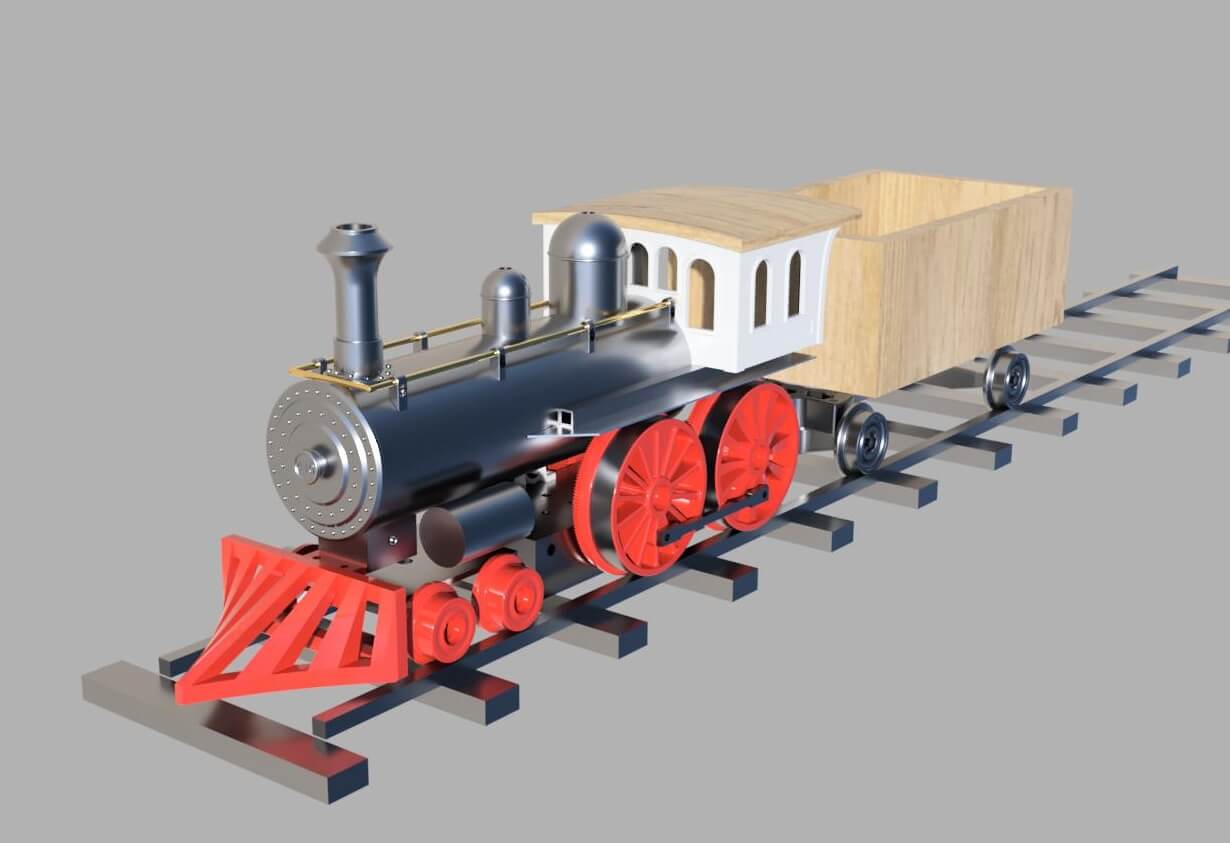
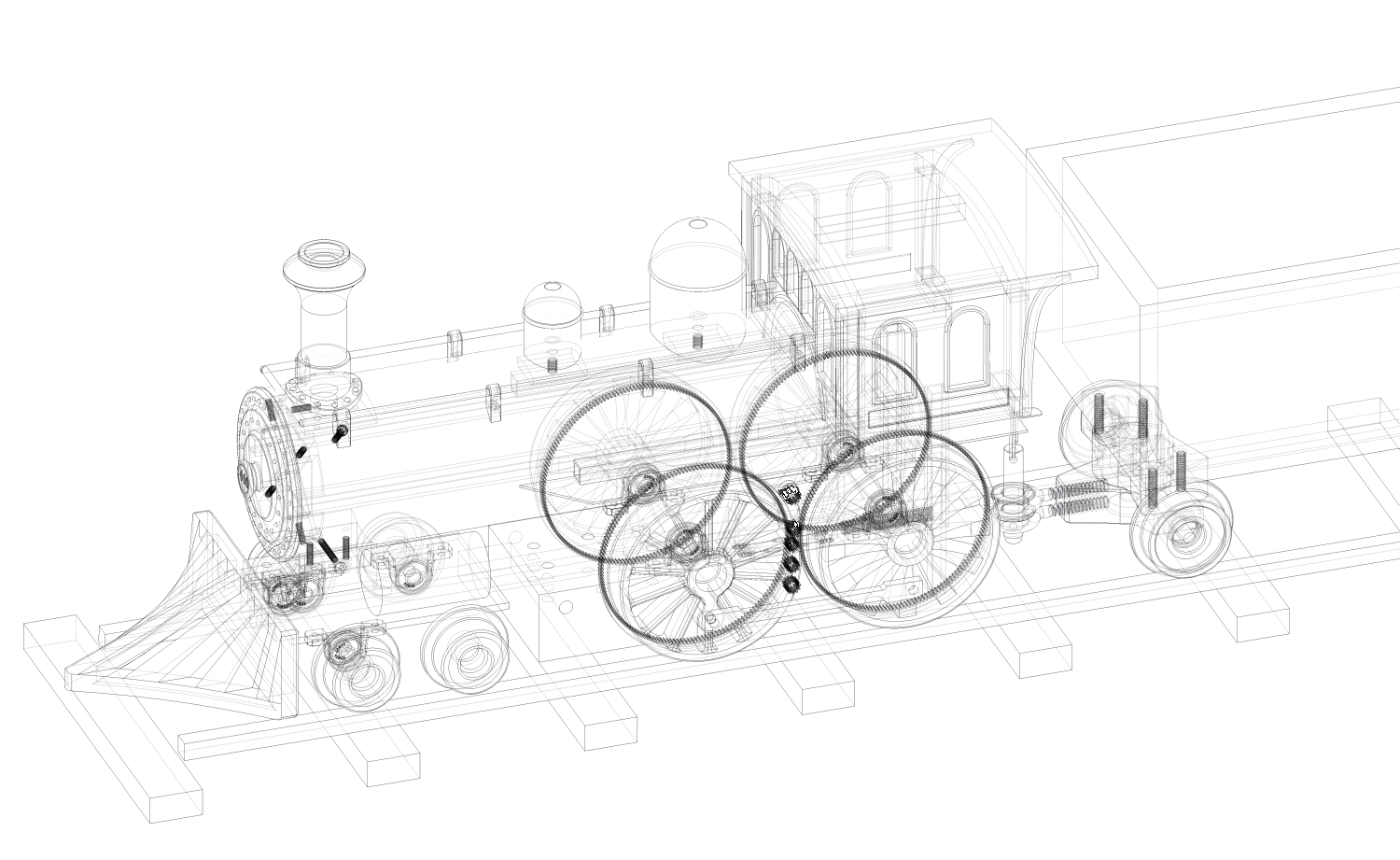
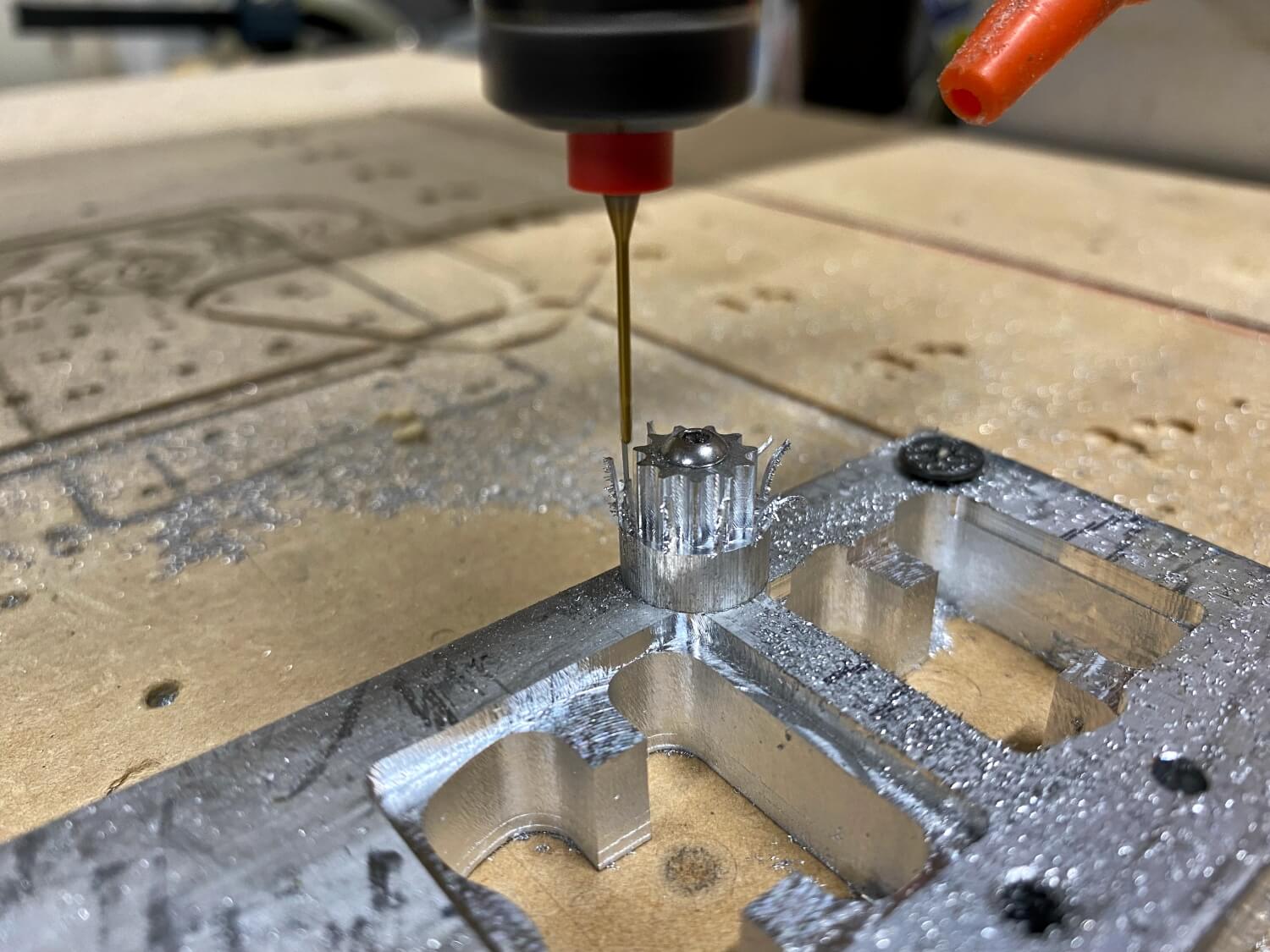
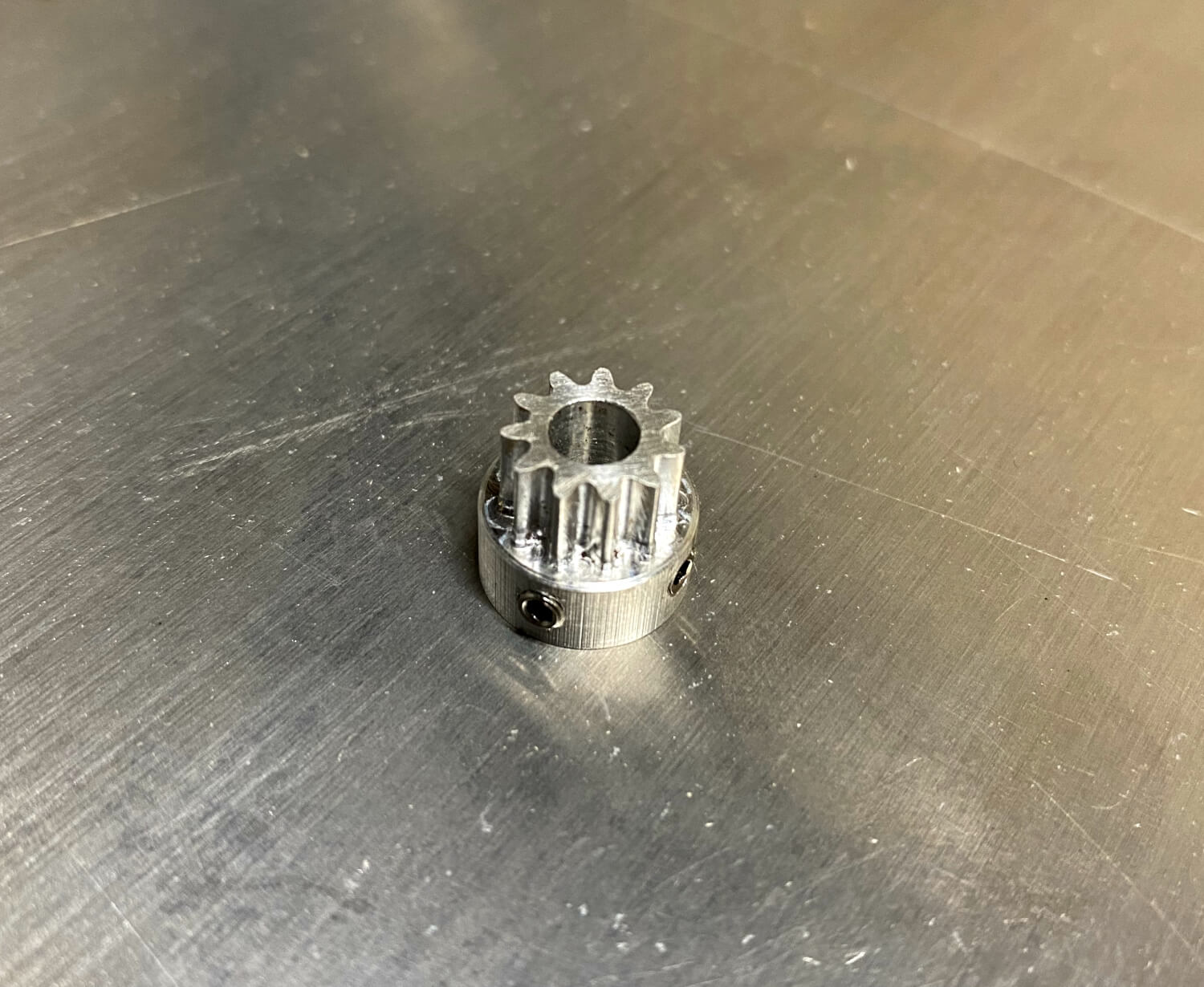
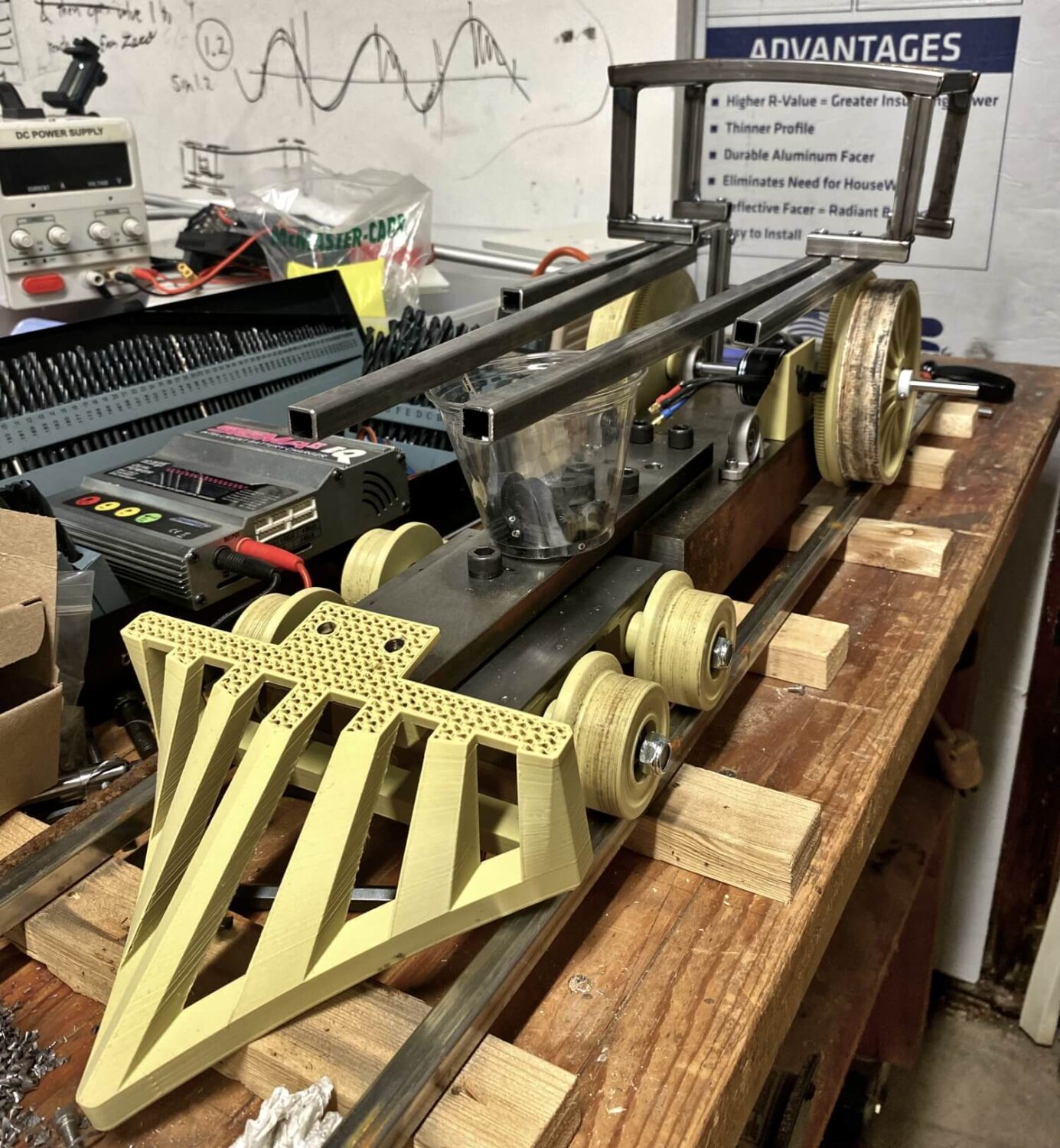
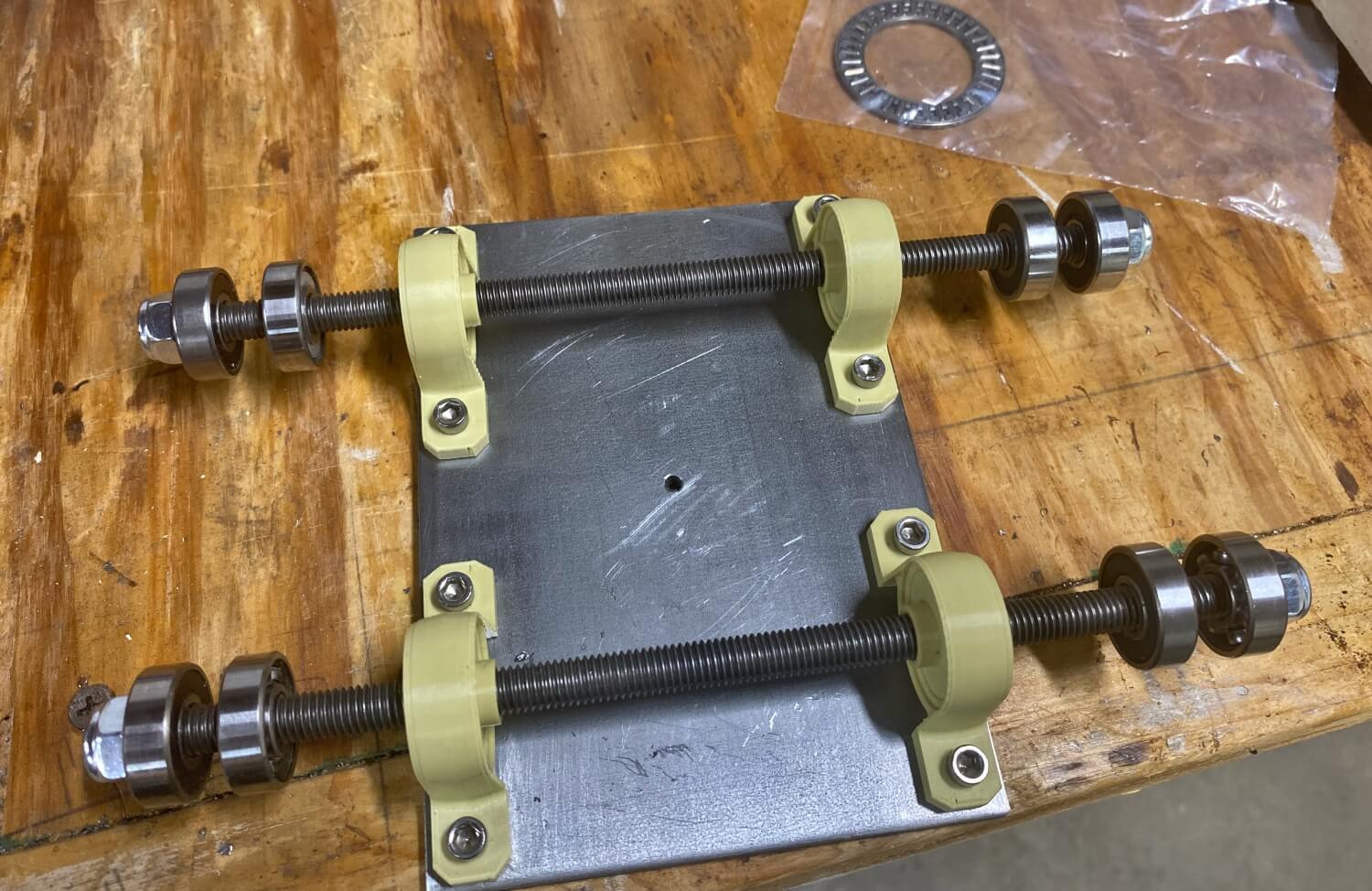
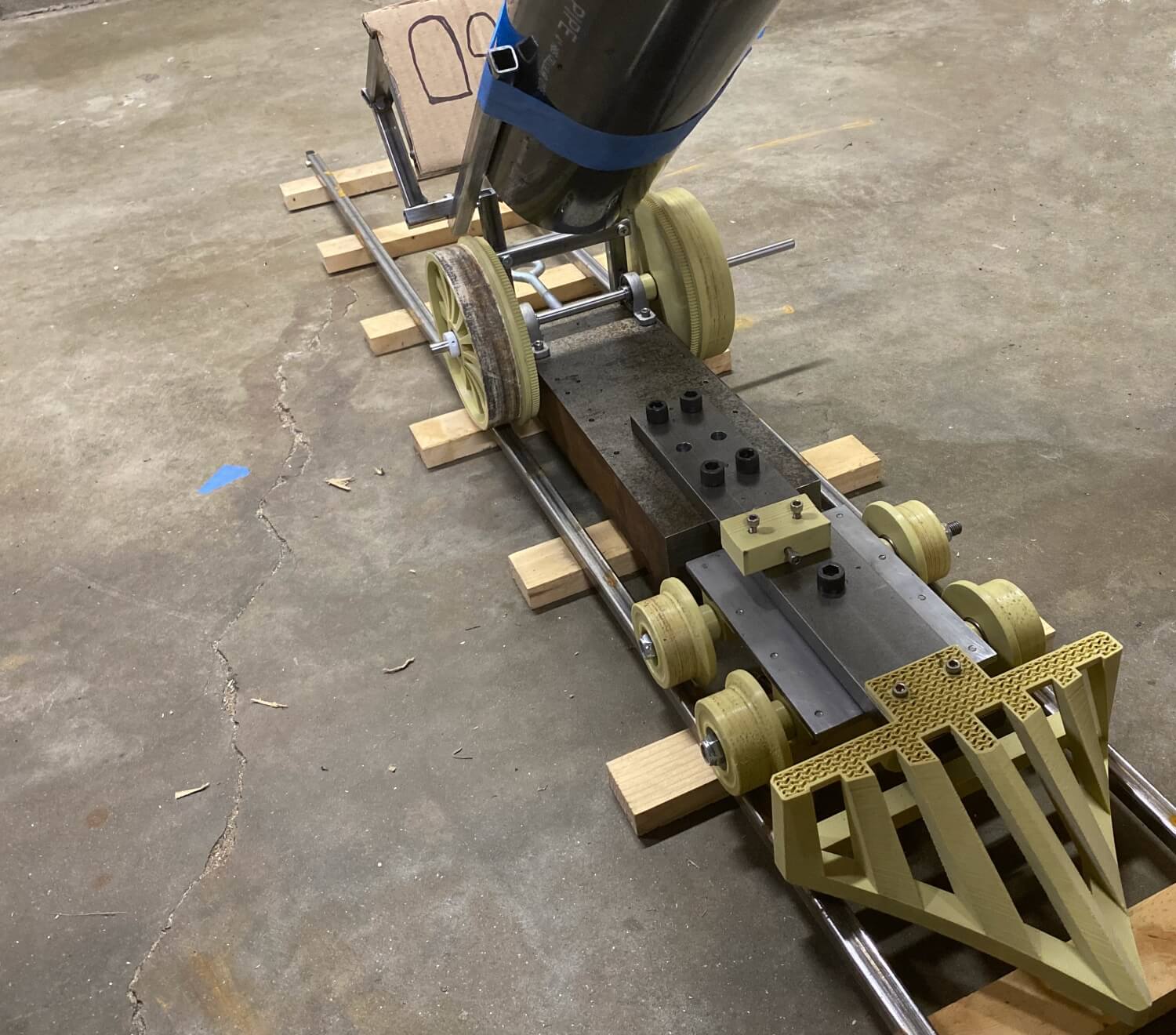
The engine took 3 weeks to design and build after acquiring a large block of steel for the chassis. The next main component was the sub-frame composed of a .5x2x12 steel square stock bolted to the main chassis and supporting a plate on a needle bearing for the 2 front axles. the front and rear axles are supported by 8mm pillow blocks. the wheels use 2 608 bearing each. the boiler is 4″ abs tube with the steel framed cab running lengthwise down the tube. Over the welded cab there is a 3d print for the front and sides while the top is plated with a .0625″ aluminum sheet and skinned with 3ply plywood. Trim such as the smoke stack is 3d printed with a supported metal tube. The drive train consists of a 700W brushless outrunner, vesc speed controller, and 5000mah 3s lithium battery. The Pinion is an 11t aluminum gear driving to the wheel with 140t. The track took about 3 month of on and off work with the most significant amount of time dedicated to making a rolling tubing bender to create the turned pieces. Since the track is not easily retained a few methods were tested to hold the tracks to the ties. most notably pre-drilling the holes on the ties and pressing roofing nails to a depth .2″ above the tie resulted in the ability to press the steel between the nails dogearing the heads and preventing the track from coming easily back out. While this worked it proved to be a problem for the train wheel geometry as it protrude too close to the top of the steel and could collide with the wheels of the cars or engine. Reluctantly self tapping screws were used to hold the ties to the track and while it not able to be assembled from the top down it is very fast and provides a lot of holding strength. Aver all this project took about 4 months and while I’m not sure I would do it again I’m sure I will be back to this project at some point to work on the laundry list of things I wanted to do but didn’t.
EX:
Engine sounds via speaker in boiler
Humidifier for smoke stack
Headlight
Dual motor
Connecting rod for dual drive wheel
Paint
Internal controls
Proximity safety system
Steel banded wheels